Broken machines don’t just cost money – they steal time, create stress, and kill productivity. In 2024, businesses faced significant losses due to unexpected downtime. What stands out is that a large portion of these disruptions could have been avoided with regular preventive maintenance and a proactive preventive maintenance process.
This isn’t just about fixing things before they break. It’s about maintaining equipment, reducing safety risks, and ensuring the longevity of your critical assets. By developing a structured pm program, businesses can prevent equipment failure, improve the asset lifespan, and optimize performance. Whether you manage a small workshop, oversee large facilities with complex electrical systems, or operate within the oil and gas industry, preventive maintenance offers tailored solutions for your needs.
In this guide, we’ll show you the exact steps to build an effective preventive maintenance checklist that works. You’ll learn:
How to spot early warning signs that save thousands in repairs
Simple scheduling preventive maintenance techniques to prevent major breakdowns
Documentation methods, including maintenance history and maintenance data, to track and prevent recurring issues
Real examples of preventive maintenance strategies that extend equipment life by 40%
The difference between a well-maintained machine and a neglected one isn’t just in repair costs – it’s in reliability, efficiency, and peace of mind. With the right tools, such as a computerized maintenance management system, and support from skilled maintenance technicians, you can streamline preventive maintenance work and create effective maintenance processes. This includes managing preventive maintenance work orders and tackling tasks specific to systems like HVAC or electrical systems.
Don’t let unexpected equipment failures disrupt your workflow. Instead, invest in preventive maintenance activities to turn costly breakdowns into planned, manageable tasks. For more insights on keeping your operations running smoothly, check out our tips on effective equipment maintenance, which highlight essential practices tailored to your needs.
Step 1: Understand the Importance of Regular Maintenance
Avoid unplanned repair costs: Regular checks prevent major breakdowns.
Extend equipment life: Routine maintenance identifies problems early.
Save Money on Unexpected Repairs
Regular maintenance is a proactive strategy to keep costs down. By scheduling routine checks and repairs, companies can significantly reduce the risk of equipment failures. Unplanned maintenance is costly; when a critical machine fails, it can halt production and lead to expensive repairs. Did you know that every dollar you invest in preventive maintenance saves an average of $5 in future expenses? To further strengthen your maintenance strategy, consider exploring innovative solutions such as maintenance management software, which can enhance efficiency and streamline processes. These tools allow for better tracking of maintenance tasks and scheduling, ensuring that no step is overlooked. For more details, check out this comprehensive guide on maintenance management software and learn how it can transform your operations.
Cost of Downtime: The average cost of unplanned downtime for a large manufacturing facility is now estimated at $129 million per year.
Let’s consider the case of a manufacturing plant that invested in regular maintenance. By preventing major equipment failures, they saved thousands in repair costs. These savings meant they could invest in technology upgrades instead of emergency repairs, boosting their long-term competitiveness.
Specific Industry Examples: In the automotive sector, the cost of an hour of downtime can reach up to $2.3 million, highlighting the critical need for effective maintenance strategies to avoid such high expenses.
On the other hand, some argue regular maintenance isn’t always necessary. Businesses with non-critical or rarely used equipment may see it as an unnecessary expense. However, this approach risks higher long-term costs due to unexpected breakdowns.
Enhance Equipment Lifespan
Equipment is expensive, and ensuring its longevity is critical for cost management and operational success. A preventive maintenance program can significantly extend asset lifespan, protecting your investment and reducing maintenance costs. This proactive approach focuses on scheduled maintenance and preventive maintenance tasks to prevent costly equipment failure and unexpected breakdowns.
Factors like operating conditions, maintenance practices, and environmental factors all impact the durability of critical assets. For example, HVAC systems or electrical systems in harsh environments require frequent preventive maintenance work to avoid premature wear. By implementing a preventive maintenance checklist, you can identify areas that need attention and ensure maintenance technicians perform the necessary maintenance tasks on time.
Skepticism around regular maintenance often stems from the perception that it requires more labor. However, the benefits of preventive maintenance far outweigh the downsides. With a well-structured pm program, you can avoid unexpected equipment failures, lower maintenance costs, and improve overall efficiency.
Regular attention might not always catch emerging issues immediately, but it dramatically reduces risks and delivers substantial cost savings. Think of it as an insurance policy against failures, helping businesses maintain their asset management goals. This balance is why informed decisions and accurate data, often enabled by preventive maintenance software, are essential.
Equipment Lifespan: Preventive maintenance can prolong the life expectancy of equipment by 20% to 40%.
Whether from a cost-saving angle or longevity perspective, regular maintenance proves its worth. Companies that embrace this approach not only save money but also ensure smooth and efficient operations.
For further exploration, resources like “Uptime” by John D. Campbell and podcasts such as “Asset Management Professionals” offer comprehensive insights into maximizing equipment efficiency.
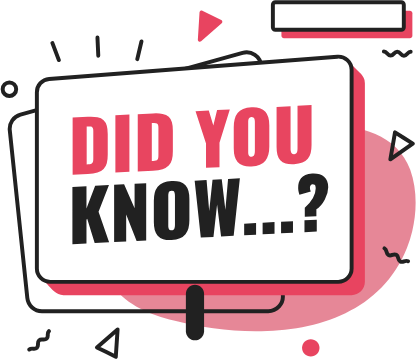
The average Metrobi driver rating is 4.97 / 5.00
Metrobi drivers are highly rated by local businesses for their professionalism and reliability, giving you peace of mind with every delivery.
Step 2: Implement A Cost-Effective Preventive Maintenance Program
Prevent breakdowns and save money with planned maintenance.
Focus on critical equipment to stretch your budget.
Prepare for inspections with a well-planned schedule.
Develop a Preventive Maintenance Schedule
Establishing a maintenance schedule is key. Start by creating a calendar to lay out routine checks. This helps keep track of when each piece of equipment needs attention.
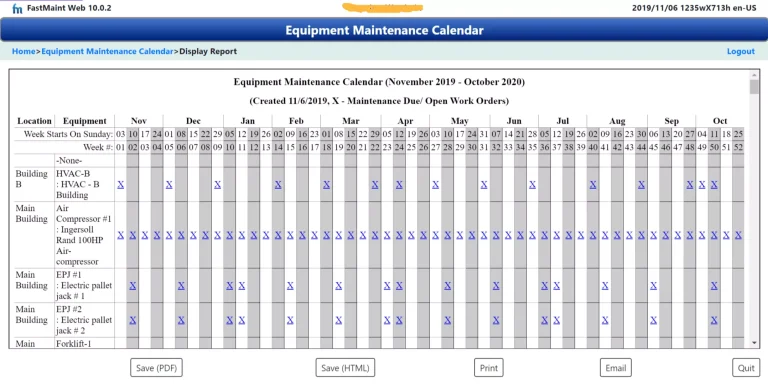
Identify Equipment Needs
List all equipment that requires regular checks. This includes both high-usage machinery and those that play a critical role in operations. Understanding what needs checking ensures nothing is left out.Determine Frequency
Decide how often each item on the list should be checked. For high-use equipment, consider weekly or monthly checks. For less critical items, quarterly might do. Look at records to find what works best.Allocate Specific Times
Choose specific days and times for each check. Align these with operational downtimes to minimize interruptions. Ensure that staff are available to conduct the checks.Communicate and Document
Share this calendar with your maintenance team. Documentation ensures everyone knows the schedule. Use software like Google Calendar or specialized maintenance tools for alerts and updates.
Allocate Time for Inspections and Minor Repairs
Inspections and minor repairs are part of the schedule. Each inspection should allow enough time for minor repairs. This can prevent small issues from becoming costly later.
Allocate Additional Time
Add extra time for each scheduled inspection. Surprises can happen, so having a buffer keeps you from rushing through checks.Prepare for Repairs
Ensure that tools and parts for common repairs are ready. This reduces downtime by allowing minor repairs during inspection.
Set Priorities in Preventive Maintenance Tasks
With a schedule in place, set your priorities. Not all equipment needs the same level of attention. Focus first on high-use machinery that impacts productivity.
Evaluate Equipment Importance
Rank each piece based on usage and role in production. Equipment critical to daily operations needs more frequent attention. Those with less impact can be checked less often.Assess Maintenance Needs
Look at historical data for frequent breakdowns or issues. Prioritize equipment with past problems. This data-driven approach helps focus efforts where they’re needed most.Balance Needs and Benefits
Balance immediate demands with long-term planning. It’s tempting to focus only on urgent repairs, but proactive checks prevent future issues. Allocate resources to achieve both goals.Adjust as Needed
Review and adjust priorities regularly. Operations change, and so should your maintenance focus. Regular reviews ensure alignment with current business needs.
By developing a maintenance schedule and setting clear priorities, organizations can implement cost-effective strategies that support long-term savings and operational efficiency.
Step 3: Reap the Benefits of Preventive Maintenance
Maintenance done on time saves money by preventing bigger problems.
Different types of maintenance meet different equipment needs best.
Understanding maintenance types can help avoid unnecessary work and costs.
Cost Savings from Maintenance Strategies
Predictive Maintenance: Companies implementing predictive maintenance can achieve cost reductions of 18% to 25% compared to traditional preventive maintenance practices.
Proactive Maintenance: Organizations that invest in proactive maintenance strategies can reduce equipment downtime by as much as 85%.
Reactive vs. Predictive Maintenance: Companies relying on predictive maintenance experience 52.7% less unplanned downtime and 78.5% fewer defects compared to those using reactive maintenance.
Cost-Benefit Analysis: Investment in predictive maintenance technologies can generate returns of up to 10 times the initial cost, primarily through reduced repair costs and extended equipment. lifespan
Unscheduled Downtime Costs: Manufacturing and process industries lose between $20 billion and $60 billion annually due to unscheduled downtime.
1. Time-Based Maintenance
Time-based maintenance involves performing preventive maintenance tasks at scheduled intervals, regardless of equipment condition. For instance, machines like a printing press that operates daily can follow a preventive maintenance schedule with monthly inspections. This type is particularly effective for equipment with consistent wear patterns.
The advantages include consistent performance and reduced risks of equipment failure. However, it may lead to unnecessary downtime for scheduled maintenance when no immediate issues exist. Books like Maintenance Planning and Scheduling Handbook by Richard D. Palmer offer insights into balancing these challenges.
2. Usage-Based Maintenance
Usage-based maintenance tailors preventive maintenance work to equipment usage levels, such as hours operated or miles traveled. This approach helps allocate resources efficiently, ensuring heavily used machinery receives attention without over-maintaining lesser-used equipment.
This system prevents wasteful repairs while focusing on critical areas, providing better maintenance practices and reducing costs. However, it requires accurate data collection, often supported by predictive maintenance tools and maintenance data tracking.
3. Condition-Based Maintenance
Condition-based maintenance uses real-time monitoring to assess equipment health. For example, vibration analysis can detect wear in rotating machinery before it becomes critical. This approach minimizes downtime by ensuring proactive maintenance occurs only when necessary.
Organizations benefit from the increased availability of critical assets, making it an essential part of modern asset management. Resources like Reliability-Centered Maintenance by John Moubray offer detailed strategies for implementing this method.
4. Predictive Maintenance
Predictive maintenance leverages advanced analytics and machine learning to forecast when failures might occur, enabling maintenance teams to act before issues arise. This strategy transforms reactive approaches into proactive maintenance strategies, extending asset lifespan and reducing unplanned downtime.
Although it requires significant upfront investment in preventive maintenance software and systems, the long-term savings are substantial. Beginners can explore Predictive Maintenance 4.0 by Nivash Jeevanandam for practical applications of this technology.
5. Calendar and Run-Time Based Maintenance
This hybrid approach combines time-based and usage-based models, making it suitable for equipment with variable usage patterns. Backup generators, for instance, benefit from periodic inspections regardless of usage, ensuring reliability during emergencies.
With adaptability and precision, this method supports the maintenance of critical assets like HVAC systems or electrical systems. However, it demands robust scheduling and resource allocation to balance costs and benefits. Books like The Equipment Management Handbook by Samuel L. Lewis provide valuable insights into this strategy.
By understanding and applying these types of preventive maintenance, businesses can optimize their maintenance processes, enhance asset management, and significantly reduce downtime. In the next section, we’ll explore how to integrate these methods into your operations to achieve greater efficiency and savings.
Step 4: Employ Top Preventive Maintenance Techniques
Regular checks keep machinery working smoothly and prevent breakdowns.
Keep records. They reveal patterns and problems.
Follow practical steps to prevent costly repairs and keep equipment running longer.
1. Regular Inspections
Performing inspections regularly ensures equipment stays in top shape. Begin by setting a schedule. This schedule should include frequent visual and operational checks. A visual inspection often spots issues like corrosion, cracks, and leaks. Operational checks, on the other hand, help detect abnormal sounds or vibrations during use. Both types help identify early signs of wear and tear. Documentation of inspections is essential. Note any findings as written records ensure problems get fixed before they cause costly interruptions.
Consistency is key. Make sure inspections happen routinely. For example, conduct daily checks on high-use equipment and weekly inspections on less critical machinery. Make use of checklists for each inspection. These tools help ensure no part of the equipment is overlooked during checks. If you’re new to crafting checklists, start with basic components such as checking bolts, wires, or hydraulic lines. A good checklist can reduce inspection time and improve accuracy.
2. Documentation and Tracking
Thorough documentation is a staple of effective preventive maintenance. Each inspection must have a detailed report. It’s crucial to note what was checked, what was found, and any steps taken to fix issues. Consistent record-keeping helps to track equipment performance over time. These records provide vital data that highlights recurring issues or helps forecast future maintenance needs.
Use digital tools for documentation. Many organizations have started adopting software solutions for easier tracking and analysis. This is part of the broader industry move towards utilizing technology for better maintenance management. Digitizing records can make it easier to access and analyze them, enabling teams to see patterns and trends quickly.
3. Scheduled Cleaning and Lubrication
Regular cleaning and lubrication are simple yet critical tasks. Schedule these activities to avoid premature wear. Machines that are clean run cooler and more efficiently. Dirt and grime accumulation can lead to overheating or component failures. Similarly, lubrication reduces friction among moving parts, preventing wear and extending equipment life.
Create a cleaning and lubrication schedule tailored to each piece of equipment. Machines operating under harsh conditions may need more frequent actions. Use manufacturer guidelines as a reference for specific lubrication requirements. Logs should include details about the types of lubricants used and any cleaning chemicals applied. These logs ensure adherence to the maintenance plan.
4. Calibration and Adjustment
Calibration ensures precision where machinery is involved. Regular calibration helps maintain the accuracy of equipment. For example, manufacturing equipment often loses precision over time, affecting product quality. Schedule calibration based on equipment use and manufacturer recommendations.
Adjustments are necessary when parts become loose or misaligned through regular use. Check for misalignments and imbalances during routine inspections and correct any detected immediately to prevent further damage. Have trained personnel perform these tasks, as improper adjustments may lead to bigger issues down the line.
5. Staff Training
A well-trained staff is vital for effective preventive maintenance. Conduct regular training sessions to keep everyone updated on the latest maintenance techniques and safety standards. Training should cover how to conduct inspections, interpret documentation, and perform basic adjustments and lubrication. It’s essential that everyone can recognize common warning signs of mechanical issues.
Ongoing education helps bridge gaps in skills. Lack of resources, including qualified personnel, is a common challenge, affecting nearly half of facilities, making regular training sessions indispensable.
In conclusion, applying these preventive maintenance techniques is crucial. They help save money and extend machinery life. Moving forward into further refinements and more advanced maintenance practices will only boost efficiency and reliability in the long run.
Advanced Tips for Optimizing Your Maintenance Plan
Real-time monitoring enhances equipment health.
Avoid routine traps for smoother operations.
Boost decision-making with comprehensive analysis.
Explore New Technologies: Preventive Maintenance Software
Looking to fine-tune your maintenance plan? Leveraging new technologies provides an edge. Real-time data-gathering tools, like Internet of Things (IoT) sensors, offer constant updates on equipment health. These sensors detect early warning signs, eliminating guesswork. By catching issues early, costly repairs are avoided, keeping operations running smoothly.
Software solutions also play a crucial role. They track maintenance needs, scheduling, and resource allocation, reducing downtime significantly. Options like IBM Maximo or UpKeep not only track wear and tear but ensure that your team is on the same page. Books like “Maintenance Planning and Scheduling Handbook” by Richard D. Palmer push these ideas further, giving a comprehensive overview of how software assists in maintenance optimization.
When deciding on tech investments, evaluate the long-term benefits. Critics argue that high initial costs deter businesses. But, the reduction in downtime and repair expenses presents a strong case for embracing tech. Further exploration can be done through online resources, technical magazines, and forums dedicated to maintenance optimization.
Common Pitfalls and How to Avoid Them
Maintenance plans often overlook low-value equipment, assuming it’s not worth the effort. However, this gear, which might include conveyors or support structures, ensures workflow efficiency. Missteps can bottleneck operations, creating unnecessary slowdowns. Michael Blanchard, a maintenance guru, emphasizes that all equipment, regardless of value, deserves attention to minimize failures in equipment lower down the line.
Teams face another challenge: ensuring consistency in routines. Disparate methods across teams lead to irregular maintenance, causing inconsistency in performance. Having a unified approach, with standardized protocols and clear communication, mitigates this risk. Regular meetings and interdepartmental audits ensure everyone adheres to the strategy. Complete consistency is challenging but not impossible; books such as Keith Mobley’s “Maintenance Fundamentals” provide more insights into achieving it.
Invest in Staff Training and Development
A well-trained team adapts to plan changes effortlessly. Training must go beyond mere technical know-how. It should include new developments in maintenance techniques and the software used in the process. Offering certifications is a bonus, motivating staff while ensuring they’re capable of handling the latest technology and methodologies.
Courses on platforms like Coursera and Udemy provide a range of topics from basic to advanced maintenance management. Experts argue against ignoring staff development due to cost concerns, asserting that training investments yield significant returns in operational efficiency and equipment lifespan. For more insightful strategies, delve into “Maintenance Management Auditing” by Edward H. Hartshorn, which places a strong emphasis on educating and empowering teams efficiently.
Harness Data to Drive Decisions
Companies sitting on vast amounts of data often ignore it due to the complexity of analysis. Yet, decoding this data produces big wins. Comprehensive data analysis highlights trends, revealing patterns of frequent breakdowns or wear. Predictive insights lead to informed decisions on maintenance scheduling.
For those wishing to go deeper into data analysis, resources like “Data-Driven Maintenance” by Martin Mulder reveal how properly analyzed data informs better planning. Critics argue that an over-reliance on data can lead managers to miss signs visible only in physical inspections. A balanced approach, with both data and physical checks, ensures comprehensive coverage.
Collaborate Across Departments
Collaboration fosters an environment where maintenance isn’t isolated. By connecting with production, HR, and financial departments, shared goals and resources become accessible. This synergy optimizes resource use and aligns objectives, creating a holistic equipment management strategy.
Bi-monthly cross-departmental review meetings keep everyone aligned, with clear responsibilities outlined. Publications like “The Lean Management Handbook” by Debashis Sahoo stress the importance of cross-functional collaboration in managing maintenance. Engaging with these insights solidifies your understanding of an optimized maintenance approach.
These advanced tips form the backbone of a fine-tuned maintenance plan, driving efficiency and savings.
Troubleshooting Common Issues
Early identification of problems prevents costly downtime.
Focus on key areas might lead to faster solutions.
Early intervention boosts equipment life and reliability.
Identify Warning Signs Early
Early warning signs are key to troubleshooting. Recognizing them can be the difference between a quick fix and a costly emergency. The top five signs of machine failure include abnormal sounds, unclean components, unnecessary vibrations, excessive heat, and performance decline. Abnormal noises, such as grinding or squealing, often suggest mechanical issues, while overheating may signal problems like inadequate lubrication or electrical faults. Being aware of the critical points in machinery is crucial. Focus on components like bearings, seals, and joints—areas prone to stress and failure. Regular observation of these parts ensures they’re functioning as expected and keeps machines running smoothly.
Condition-based monitoring can be a game-changer. Techniques like vibration analysis and oil analysis provide insights into machinery health. This approach allows for early identification of problems and helps avoid more severe breakdowns. Engineers should carefully observe every part of the equipment using their senses (eyesight, smell, hearing) to identify signs of faulty equipment, such as overheated components, loose components, or unusual smells and sounds. Real-time data collection, such as continuous monitoring of vibration, temperature, and lubrication levels, significantly reduces failure risks and ensures smooth operations.
Pinpointing Problem Areas
When a failure seems imminent, pinpointing problem areas helps narrow down the cause. Compare current performance with baseline conditions to spot deviations. Compare specific parts against their ideal state. Narrowing the focus saves time on testing and leads to quicker resolutions. For instance, if machine output is lagging, examine critical components first. Problematic parts are often those with frequent wear.
Analyzing performance data helps identify anomalies. For a deeper dive into effective data use, consider The Value of Machine Data for Quoting about using machine data. This can help draw connections between performance dips and potential failures. Books like “Maintenance Engineering Handbook” by Lindley R. Higgins offer strategies for analyzing failure patterns and improving troubleshooting techniques. This comprehensive resource provides an in-depth look at maintenance practices beyond basic troubleshooting, offering details on common equipment issues and solutions. By exploring these resources, you can further understand your machinery’s health and improve your facility’s efficiency.
Weighing the Benefits of Continuous Monitoring
Is continuous monitoring worth the investment? There’s a strong case for it. Real-time data collection not only identifies existing problems but also anticipates future issues. This proactive approach is unlike traditional time-based checks, which might miss subtle changes. With real-time insights, maintenance can be scheduled before a failure occurs, reducing downtime considerably.
However, it’s important to consider potential drawbacks. Initial costs for setting up monitoring systems can be high. This approach requires significant investment in technology and training.
Finally, communication across departments ensures problem-solving isn’t isolated. By encouraging collaboration, teams deliver faster results. Regular meetings and shared logs can keep everyone informed. This holistic approach reduces blind spots and uncovers solutions faster.
Further Resources and Reading
Advanced maintenance software can streamline practices.
Predictive maintenance techniques can enhance efficiency.
Related Topics or Advanced Guides
Advanced maintenance software options can significantly improve operational efficiency by automating tasks like scheduling, inventory management, and predictive analysis. Platforms like Maintenance Connection and eMaint offer features that can integrate with existing systems and enhance the functionality of maintenance programs. These platforms use data-driven insights to anticipate equipment needs, minimize downtime, and optimize resources. For professionals looking to incorporate software into their maintenance strategy, “Maintenance Management: Make a Data-Driven Approach with IoT and Machine Learning” is an excellent book that delves into how technology can refine maintenance practices.
Predictive maintenance, a step beyond preventive approaches, uses real-time data to predict when equipment might fail. This method saves time and money by addressing issues before they escalate. Techniques involve vibration analysis, thermal imaging, and ultrasonic testing. The pros are significant: reduced downtime, reduced maintenance costs, and increased equipment lifespan. However, they do come with costs such as setup and training. The 2023 white paper “Predictive Maintenance with Machine Learning: The Next Step in Asset Management” is a valuable resource to understand these techniques in depth.
Why Preventive Maintenance Matters
Regular preventative maintenance significantly reduces downtime, which is crucial for maintaining consistent production levels. The reduction in unexpected breakdowns translates to less stress for maintenance teams and higher reliability for operations.
Preventive Maintenance Cost Benefits: Companies that invest in preventive strategies often report a 25–30% reduction in maintenance costs. Additionally, for every $1 invested in preventive maintenance, companies can save between $4 and $9 in repair and replacement costs.
Another crucial benefit is the support of a sustainable work environment. Consistent attention to equipment not only increases reliability but also has environmental benefits, like less frequent replacements. By ensuring that machines run efficiently, energy usage is reduced, contributing to a smaller carbon footprint. “The Green Industrial Revolution: Sustainable Practices in Maintenance” provides a comprehensive guide to achieving sustainability through thoughtful maintenance strategies.
Conclusion
Regular maintenance saves money. This is not a theory – it’s a proven business practice. By following the steps in this guide, you can stop spending money on expensive repairs caused by equipment failure and start investing in a preventive maintenance plan.
Think of preventive maintenance as a long-term money-saving strategy. When you check equipment regularly, fix small issues early, and keep good records, you’re not only avoiding unexpected equipment failures but also implementing a preventive maintenance strategy that protects your investments.
Small actions add up to big results. Start with one piece of equipment. Create a simple maintenance schedule to avoid costly reactive maintenance. Document what you do and learn about different types of preventive maintenance that can optimize performance. Then, expand your program step by step.
The choice is clear: spend a little time and money now on prevention, or pay much more later for emergency repairs. Understanding why preventive maintenance is important isn’t just about avoiding problems – it’s about taking control of your equipment’s lifespan and your budget.
Take action today. Pick one machine or system. Schedule its first maintenance check. Write it down. This small step will start saving you money right away while reducing the risk of unexpected equipment failures. Your future self will thank you for making this smart financial decision.