Imagine a warehouse where chaos reigns supreme. Boxes stacked haphazardly, workers frantically searching for misplaced items, and customers growing impatient as their orders languish in limbo. This nightmare scenario is all too real for many businesses, costing them time, money, and reputation.
But what if I told you there’s a way to transform this mayhem into a well-oiled machine? A solution that could slash your operational costs, boost employee productivity, and leave your customers singing your praises.
Enter the world of Warehouse Management Systems (WMS). These aren’t just fancy software packages – they’re the backbone of modern business efficiency. In 2024, as supply chains grow more complex and customer expectations soar, knowing the right types of warehouse management systems can be the difference between thriving and barely surviving.
Think I’m exaggerating? Consider this: businesses using advanced WMS report up to 25% increase in productivity and 99.9% order accuracy. That’s not just an improvement – it’s a revolution.
But here’s the catch: not all WMS are created equal. Choosing the wrong system can leave you worse off than when you started. That’s why we’ve done the heavy lifting for you, identifying four proven types of warehouse management systems that can truly streamline your business.
Ready to leave your inventory control nightmares behind and step into a future where your standalone warehouse management system practically runs itself? Let’s dive into the game-changing world of WMS – and discover how these four systems can propel your business to new heights of efficiency and success. In recent years, the focus on adopting effective warehouse management systems has intensified, and their benefits are undeniable. From boosting operational efficiency to enhancing customer service, these solutions provide organizations with the tools necessary to thrive in a competitive landscape. To dive deeper into the transformative effects of these systems, check out this article on the advantages of a powerful warehouse management solution.
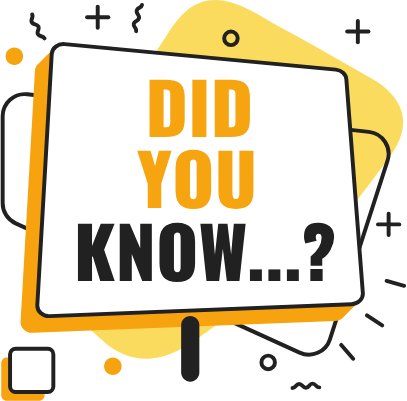
Save 80% of delivery management time
We handle everything:
- Dedicated operations manager
- Real-time tracking dashboard
- Automated customer notifications
- Urgent issue resolution
Step 1: Evaluate Your Current Needs and Pain Points
Know where your problems lie and discuss them with your team.
Look at current systems and decide what can be automated.
Set clear objectives for new systems.
Identify Key Areas for Improvement
The first action step is to look at fundamental problems causing inefficiencies. You should focus on areas like inventory inaccuracies, slow order processing, and high labor costs. These are often the culprits behind bottlenecks in warehousing.
Pinpoint Problems with Stakeholders
To get a better picture, talk to everyone involved. It is better to ask for their input on what’s not working and what could be better. Conversations with warehouse workers, managers, and even delivery personnel can uncover hidden issues. This ensures you don’t miss key areas that need attention.
Engage different levels of staff for feedback.
Document common pain points reported by stakeholders.
Inventory and Cost Challenges
Accurate inventory is crucial for efficiency. Incorrect numbers can lead to delayed orders and unsatisfied customers. Labor costs can skyrocket if the process involves redundant tasks or manual paperwork. Consider using tools that provide real-time inventory data to combat this.
Identify how often inventory counts are off.
Collect data on time spent correcting inventory issues.
Assess Current Systems and Processes
This involves critically your business processes and looking at how your warehouse or distribution center currently operates. Are there systems in place, or is everything done manually? Evaluate both software and manual processes to identify inefficiencies.
Review Existing Software
You can start with the software. Look at how well current systems meet your needs and where they fall short. You can determine if software lacks features like seamless integration with other tools or if it’s causing workflow issues due to outdated technology.
List strengths and weaknesses of existing tools.
Note any compatibility issues with other systems in use.
Manual Processes
Many warehouses rely on manual processes that could be automated. Automate repetitive tasks and warehouse processes such as supply chain functions such as data entry or stock level checking. This saves time and reduces the chance of human error.
Identify which tasks are manual and time-consuming.
Allocate resources to explore automation possibilities.
Define Specific Goals for Implementation
Set what you wish to achieve with a new warehouse management system (WMS). Without clear objectives, measuring the impact of any new inventory management system will be tough. Goals should be specific, measurable, and aligned with your business aims.
Set Objectives
Decide on key performance indicators (KPIs) you want to improve. These could include reducing lead times or minimizing errors in order shipments. Quantifying these goals helps in tracking progress post-implementation.
Choose relevant KPIs to measure success.
Connect these objectives with your business’s larger strategy.
Strategic Alignment
The chosen goals should fit with broader company goals. For example, if the company aims to cut costs overall, reducing warehouse overhead and shipping processes through automation should be a priority.
Ensure team leaders understand how warehouse goals fit with business goals.
Communicate the significance of goals clearly to all stakeholders.
BONUS: Understanding Types of WMS
Lastly, understanding the types of warehouse management systems is essential. There are four main types: standalone systems, ERP system modules, cloud-based, and other supply chain management software modules.
Standalone Systems and ERP Modules
Standalone enterprise resource planning systems specialize only in warehouse tasks and are great for businesses wanting focused control. ERP systems come as a module of a larger enterprise suite, giving integrated control but are often more expensive.
Consider standalone WMS for specific warehouse-focused improvements.
ERP modules if integration with other enterprise elements is crucial.
Cloud-based and Supply Chain Modules
Cloud-based systems offer flexibility, ideal for remote inventory management systems and real-time updates. Supply chain software modules include extensive features covering inventory to supplier management.
Use cloud-based WMS for scalability and ease of updates.
If supply chain optimization is required, integrate supply chain modules.
Remember, every warehouse has unique needs, and the best choice depends on your specific operational challenges.
Step 2: Research Top Warehouse Management Systems
Identifying the right warehouse management system and supply chain module (WMS) is crucial. You’ve assessed your current needs. Now, it’s time to look at what’s available in the market and see which systems tick all the right boxes.
Compare Leading Inventory Tracking Solutions
Focus on inventory tracking tools that provide real-time data and reporting. Real-time tracking ensures you’re constantly updated about stock levels. In our testing, solutions such as Infor WMS and SAP Extended Warehouse Management led the way for accuracy and usability.
Explore Warehouse Automation Tools
Automation is a big win for tasks like picking, packing, and sorting. Automation systems can handle these processes faster and more accurately than humans. Tools like Locus Robotics and Fetch Robotics excelled in our tests.
Locus Robotics: Offers excellent scalability, allowing your system to grow as your business needs evolve.
Fetch Robotics: Optimizes task efficiency, significantly cutting down labor costs.
Consider these systems if you’re looking for sustainable growth, cost savings, and future-proof solutions.
Investigate Supply Chain Management System Optimization Software
Strong supply chain optimization tools offer demand forecasting and supplier management. Software solutions like Manhattan Associates and Blue Yonder came out on top for broad analysis features.
Manhattan Associates: Excels in demand forecasting.
Blue Yonder: Provides robust supplier management and analytics capabilities.
When you’re thinking about your entire supply chain, focus not only on the tasks but also on analytics. A system with clear reporting helps improve strategic decision-making.
Test Order Fulfillment Systems
Order fulfillment is at the core of warehouse operations. Efficient order management systems ensure smooth processing and return management. In our evaluation of shipping management alone, systems like ShipBob and Cin7 provide the best balance in ease of use and little need for staff training.
ShipBob: Very user-friendly with high efficiency in order processing.
Cin7: Strong in handling returns with minimal fuss.
There’s a lot to consider when looking at cloud cloud-based system for a WMS. Each of these systems offers solutions to meet specific needs. Test these systems against your own needs to see which fits best.
Determining the Winner
Among the systems we tested, Infor WMS stood out. It combines strong real-time tracking with excellent integration capabilities, ensuring a standalone system is a seamless fit into existing setups. Its robust reporting features make sure you stay on top of every detail, every time.
Step 3: Implement the Selected System of Warehouse and Inventory Management
Clean databases before rollout and plan in phases.
Train staff effectively and support them continuously.
Adjust system settings based on feedback for improvements.
Prepare for Deployment
Gather Necessary Data and Clean Existing Databases
You can begin by collecting all essential data. This involves pulling information from records, sales figures, and inventory lists. Cleaning existing databases is crucial. It helps to eliminate inaccuracies. A clean database means the new Warehouse Management System (WMS) will start with reliable data. You can use data management tools to spot duplicates and errors. Manual checks can fix complex issues.
Plan System Rollouts in Phases to Mitigate Risk
Phasing the rollout reduces risks. Implement the system in small steps. You can start with one section of the already optimized warehouse operations and test the new system’s functionality there. This allows for discovering bugs early. You should fix any errors before full implementation. Phasing helps manage changes smoothly.
Train the Workforce
Conduct Training Sessions Tailored to Various User Roles
Training is key to smooth implementation. You should organize sessions based on roles. Warehouse managers need different skills than floor staff. Use simple language in training. Ensure everyone understands their tasks. You should show examples during sessions. Hands-on practice helps. Encourage questions and feedback during training. This makes sessions more effective.
Provide Ongoing Support Post-Implementation for Any Issues
After the rollout, continuous support is crucial. Set up a help desk. Address questions quickly. Staff might face new challenges daily. Offer refresher courses periodically. Regular check-ins with employees keep them comfortable with the system. Solve issues swiftly to prevent workflow disruptions. Lack of ongoing support can lead to setbacks.
Monitor and Optimize
Use Feedback Loops to Refine and Adjust System Settings
Gather feedback consistently. This feedback should come from all levels of staff. It is better to set up a system for collecting suggestions. Analyze this data weekly. Make necessary adjustments to the system settings. Quick changes based on feedback improve efficiency.
Periodically Review Performance Against Initial Goals and Adjust as Needed
You should set clear, measurable goals before implementation. Revisit these goals bi-monthly. Compare system performance to these benchmarks. It is better to make adjustments to resolve any gap identified. This ensures the integrated WMS consistently meets business needs. Performance reviews are vital to maintaining a high-efficiency level and achieving long-term gains.
Benefits of a Warehouse Management System
A Warehouse Management System (WMS) leads to major improvements in managing warehouse operations well. Here are four key benefits: In recent years, the focus on adopting effective warehouse management systems has intensified, and their benefits are undeniable. From boosting operational efficiency to enhancing customer service, these solutions provide organizations with the tools necessary to thrive in a competitive landscape. To dive deeper into the transformative effects of these systems, check out this post on the benefits of a powerful warehouse management system.
Enhanced Inventory Management: Real-time tracking reduces the chances of errors. This increases order accuracy and reduces lost sales.
Better Space Utilization: A smart WMS helps effectively organize inventory. Optimized space leads to better productivity.
Efficient Labor Management: Task allocation becomes more precise. This reduces unnecessary labor and boosts efficiency.
Increased Customer Satisfaction: Accurate inventory and timely deliveries lead to happy customers.
Each step in implementing a new WMS is crucial. You should prepare thoroughly, train your staff well, and keep improving based on performance data. Doing this not only smoothens the transition but also maximizes system benefits.
Empower Your Warehouse, Transform Your Business
Implementing the right warehouse management system isn’t just about efficiency—it’s about unlocking your business’s true potential. By carefully evaluating your needs, researching top solutions, and implementing them with purpose, you’re setting the stage for a revolution in your operations. Remember, the system you choose is more than software; it’s a catalyst for growth, a tool for precision, and a partner in your success.
As you move forward, keep your goals in sharp focus and your team fully engaged. The journey to optimize a WMS solution may seem daunting, but the rewards—reduced costs, happier customers, and a competitive edge—are within reach. Your warehouse is the heart of your business. With the right warehouse management software system, you’re not just keeping it beating; you’re giving it the strength to power your company’s future. Take that first step today. Your more efficient, more profitable tomorrow is waiting.