In today’s fast-paced business landscape, supply chain integration has become a critical strategy for companies seeking to optimize their operations and gain a competitive edge. But what exactly is supply chain integration, and how can it benefit your organization?
This comprehensive guide will dive deep into the concept of supply chain integration, exploring its key components, types, and the potential advantages and disadvantages it can bring to your business in 2024 and beyond. Whether you’re a supply chain professional, business leader, or simply curious about this essential topic, you’ll find valuable insights and practical tips to help you navigate the complex world of supply chain management. Interested in how freight forwarding fits into the broader supply chain management picture? Learn all about the role of freight forwarding in enhancing supply chain integration for businesses worldwide.
So, let’s explore the ins and outs of supply chain integration and discover how it can transform your business for the better.
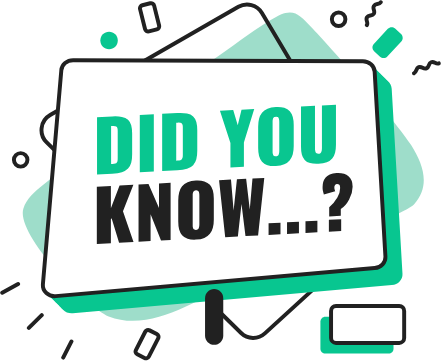
27% higher customer satisfaction
Professional delivery features:
- Real-time GPS tracking
- Automated ETA updates
- Delivery confirmation photos
- 27% higher delivery satisfaction
What is Supply Chain Integration?
Supply chain integration connects all stakeholders to optimize processes
Improves efficiency, reduces costs, and enhances customer satisfaction
Requires collaboration, information sharing, and process synchronization
Supply chain integration is connecting and coordinating all stakeholders involved in the flow of goods and services, from raw materials to material suppliers to end customers. The goal is to create a seamless, efficient, and transparent supply chain that optimizes processes, reduces costs, and improves customer satisfaction. Discover how a coordinator in logistics plays a crucial part in achieving a harmonious, cost-effective, and customer-focused supply chain network.
Market Size:
The global supply chain management market was valued at 15.85 billion U.S. dollars in recent years and is expected to reach almost 31 billion U.S. dollars by 2026.
Key components of integrated supply chain management
Collaborative planning and forecasting
Effective supply chain integration requires close collaboration between all stakeholders to plan and forecast demand accurately. This involves sharing data on sales, inventory levels, and production capacities to ensure that supply meets demand in a timely and cost-effective manner. To achieve this level of coordination and optimize your supply chain, considering the distinctions between third-party logistics (3PL) and fourth-party logistics (4PL) is crucial for informed decision-making.
Collaborative planning and forecasting tools, such as advanced analytics and machine learning algorithms, can help businesses predict future demand more accurately. By leveraging historical data and real-time market insights, companies can make informed decisions on production, inventory management, and distribution. For example, companies like Walmart and Procter & Gamble have successfully implemented collaborative planning and forecasting in their supply chains, resulting in significant improvements in efficiency and customer satisfaction.
Information sharing and visibility
Transparency and real-time information sharing are critical for supply chain integration. All stakeholders should have access to relevant data, such as order status, inventory levels, and shipment tracking, to make informed decisions and respond quickly to changes in demand or other supply chain activities.
Implementing a centralized supply chain management system, such as an ERP (Enterprise Resource Planning) or SCM (Supply Chain Management) software, can help facilitate information sharing and provide end-to-end visibility. Custom software development enables the creation of tailored ERP solutions that integrate data from various sources, such as suppliers, manufacturers, distributors, and retailers, to create a single source of truth for all stakeholders.
Process synchronization and optimization
Supply chain integration requires the synchronization significant coordination and optimization of all processes, from procurement and production to distribution and delivery. This involves identifying bottlenecks, eliminating waste, and streamlining workflows to improve efficiency and reduce lead times. Implementing construction procurement software can significantly aid in achieving these optimization goals by enhancing supply chain visibility and control.
Techniques such as Lean Manufacturing, Six Sigma, and Total Quality Management (TQM) can help businesses optimize their supply chain processes. These methodologies focus on continuous improvement, waste reduction, and customer satisfaction, which are essential for effective supply chain integration.
Types of supply chain integration
Vertical integration
Vertical integration involves the merger or acquisition of companies at different stages of the supply chain, such as a manufacturer acquiring a raw material supplier or a distributor. This type of integration allows for greater control over the entire supply chain, reducing dependence on external partners and improving efficiency.
However, vertical integration can also lead to increased complexity and reduced flexibility, as the company becomes responsible for managing multiple stages of the supply chain. It may also require significant capital investment and may not be suitable for all industries or business models.
A Side Note, Top Carbon Emitter:
Only 5% of supply chain emissions stem from direct manufacturing, whereas emissions originating within the supply chain can be 5 to 10 times greater6
Horizontal integration
Horizontal integration involves the merger or acquisition of companies in the same industry or stage of the supply chain, such as two manufacturers or two distributors. This type of integration can help businesses achieve economies of scale, increase market share, and reduce competition.
However, horizontal integration can also lead to reduced innovation and customer choice, as the merged companies may have less incentive to differentiate their products or services. It may also face regulatory challenges, particularly in industries with high levels of market concentration.
Functional integration
Functional integration involves the coordination and collaboration of different departments within a company, such as sales, marketing, and operations. This type of integration ensures that all functions are aligned toward common goals and that information flows seamlessly between departments.
Effective functional integration requires breaking down silos in identify areas and fostering a culture of collaboration and communication. This can be achieved through cross-functional teams, regular meetings, and shared performance metrics that encourage departments to work together towards common objectives.
In conclusion, supply chain integration is a critical strategy for businesses looking to optimize their operations, reduce costs, and improve customer satisfaction. By fostering collaboration, information sharing, and process synchronization, companies can create a more efficient, transparent, and responsive supply chain that delivers value to all stakeholders.
7 Benefits of Supply Chain Integration for Improved Performance
Enhanced supply chain visibility
Supply chain integration enables real-time tracking and monitoring of inventory, orders, and shipments across the entire network. By connecting data from various systems and partners, companies gain a holistic view of their supply chain operations. This visibility allows for early detection and resolution of issues and disruptions, minimizing their impact on the business. Explore how additional services can further streamline your supply chain management, elevating efficiency and bolstering client contentment.
A Major Challenge:
Only 6% of businesses achieved full supply chain visibility.
Real-time data sharing
Integrated systems facilitate the sharing of real-time data among supply chain partners. This includes information on inventory levels, production schedules, and delivery status. With access to up-to-date data, companies can make informed decisions and respond quickly to changes in demand or supply. Real-time data sharing also helps identify bottlenecks and inefficiencies, enabling continuous improvement efforts.
Optimized inventory management
Supply chain integration helps optimize inventory management by aligning supply and demand. With real-time visibility into inventory levels and customer demand, companies can reduce inventory holding costs and minimize stockouts. Improved demand forecasting and replenishment processes ensure that the right products are available at the right time and place.
Collaborative inventory planning
Integrated systems enable collaborative inventory planning among supply chain partners. Suppliers can access real-time data on customer demand and adjust their production and delivery schedules accordingly. This collaboration helps reduce excess inventory and improve inventory turns. Companies can also implement vendor-managed inventory (VMI) programs, where suppliers take responsibility for maintaining optimal inventory levels at their customers’ locations.
Operational Efficiency Gains:
A successful VMI case study demonstrated a 15% reduction in inventory costs and a 10% increase in order fulfillment.
According to a study by Supply Chain Brain, collaborative inventory planning can lead to a 10-15% reduction in inventory costs and a 5-10% increase in inventory turns. Additionally, a McKinsey report highlights the benefits of collaborative supply chain planning, including improved forecast accuracy and reduced inventory levels.
Streamlined collaborative planning
Supply chain integration facilitates streamlined collaborative planning among partners. By aligning production, distribution, and demand plans, companies can optimize resource utilization and reduce waste. Integrated systems enable real-time sharing of plans and schedules, allowing for faster response to changes in demand or other supply chain members.
Sales and operations planning (S&OP)
Sales and operations planning (S&OP) is a key process that benefits from supply chain integration. S&OP involves aligning sales, marketing, production, and finance plans to ensure that supply meets demand. Integrated systems provide a single source of truth for S&OP, enabling cross-functional collaboration and decision-making. With real-time visibility into plans and performance, companies can quickly identify and resolve gaps between supply and demand.
Stronger supplier relationship management
Supply chain integration fosters stronger supplier relationship management. By collaborating closely with suppliers, companies can engage in joint problem-solving and continuous improvement initiatives to maximize efficiency. Integrated systems facilitate the sharing of performance data and metrics, enabling joint target setting and progress tracking.
Supplier scorecards and performance management
Supplier scorecards are a powerful tool for managing supplier performance in an integrated supply chain. By defining key performance indicators (KPIs) and sharing real-time performance data, companies can hold suppliers accountable and drive continuous improvement. Integrated systems automate the collection and reporting of supplier performance data, reducing manual effort and ensuring data accuracy.
According to Supply Chain Digital, effective supplier performance management can lead to a 20-30% reduction in costs and a 10-20% improvement in quality. Additionally, Thomasnet highlights the benefits of supplier performance management, including improved supplier relationships and reduced risk.
Increased operational efficiency
Supply chain integration increases operational efficiency by eliminating redundant processes and waste. Integrated systems automate manual tasks and enable the digitization of paper-based processes. This reduces errors, speeds up cycle times, and frees up resources for higher-value activities.
Lean supply chain practices
Lean supply chain practices, such as just-in-time (JIT) delivery and continuous improvement, are easier to implement in an integrated supply chain. With real-time visibility into demand and inventory levels, companies can optimize production schedules and minimize inventory holding costs. Integrated systems also facilitate the sharing of best practices and improvement ideas across the supply chain, driving efficiency gains.
Faster time-to-market
Supply chain integration enables faster time-to-market for new products. By collaborating closely with suppliers during the design and development phases, companies can ensure that new products are designed for manufacturability and supply chain efficiency. Integrated systems facilitate the sharing of product specifications, test results, and production plans, reducing the risk of delays and quality issues.
Multi-Shoring on the Rise for Risk Management:
The IDC analyst predicts that by 2024, 50% of companies will have implemented more balanced multi-shoring sourcing strategies to better address risk.
Concurrent engineering
Concurrent engineering is a product development approach that involves cross-functional teams working in parallel to design, test, and manufacture new products. Supply chain integration supports concurrent engineering by enabling real-time collaboration among internal teams and external partners. Integrated systems provide a single source of truth for product data, ensuring that all stakeholders are working with the latest information.
A study by ResearchGate found that concurrent engineering can reduce product development time by 30-50% and improve product quality by 20-30%. Additionally, a ScienceDirect article highlights the benefits of concurrent engineering, including reduced costs and improved collaboration.
Improved customer service
Supply chain integration improves customer service by enabling reliable on-time delivery and order fulfillment. With real-time visibility into inventory levels and production schedules, companies can provide accurate delivery promises to customers. Integrated systems also enable personalized offerings and experiences based on customer preferences and purchase history.
A Top Supply Chain Priority:
83% of businesses prioritize customer experience enhancement in digital business strategy for supply chains.
Collaborative demand planning
Collaborative demand planning involves working closely with customers to understand their needs and preferences. By integrating customer data into supply chain planning processes, companies can improve forecast accuracy and ensure that the right products are available when and where customers need them. Integrated systems facilitate the sharing of point-of-sale (POS) data, enabling companies to respond quickly to changes in customer demand.
8 Potential Drawbacks and Risks of Supply Chain Integration
High Implementation Costs
Implementing supply chain integration is a significant undertaking that requires substantial investments in technology, infrastructure, and change management. Companies must allocate resources to upgrade their systems, establish secure data exchange protocols, and train employees on new processes. These upfront costs can be a major barrier to internal integration, especially for smaller organizations with limited budgets.
Moreover, the transition to an integrated supply chain can cause temporary disruptions to existing operations. As companies adapt to new workflows and technologies, there may be a period of reduced efficiency and productivity. This can lead to missed deadlines, order fulfillment issues, and customer dissatisfaction, all of which can impact the bottom line.
Increased Dependency on Partners
While collaboration is a cornerstone of supply chain integration, it also creates a heightened level of dependency on partners. When critical functions are shared across the network, companies become more vulnerable to disruptions caused by partner failures or missteps. For example, if a key supplier experiences a production shutdown or a logistics provider faces capacity constraints, the entire supply chain can suffer.
This interdependency also reduces flexibility in partner selection and management. Once deeply integrated, it becomes more difficult and costly to switch partners or adjust the network structure. Companies may find themselves locked into suboptimal relationships or unable to quickly adapt to changing market conditions.
Loss of Control and Transparency
Supply chain integration often involves relinquishing some degree of control over certain processes and decisions. As companies rely more heavily on partners for critical data and insights, they may lose visibility into key metrics and performance indicators. This can make it challenging to identify problems, track progress, and make informed decisions. Curious about how third-party logistics providers can impact supply chain visibility? Explore the role of 3PL in enhancing or complicating supply chain integration.
Furthermore, the increased sharing of sensitive information across the network can create opportunities for opportunistic behavior or misaligned incentives. Partners may prioritize their own interests over the collective good, leading to trust issues and conflicts. Establishing clear governance structures, performance metrics, and incentive systems is crucial to mitigate these risks.
Integration and Compatibility Challenges
One of the most significant hurdles in supply chain integration is the need to harmonize disparate systems, processes, and cultures across partners. Each company may have its own unique technologies, data formats, and operating procedures, making seamless integration a complex undertaking. If overcoming these supply chain challenges is your goal, explore leading third-party logistics providers that can ensure smooth and efficient integration across various systems and operations.
Achieving true interoperability often requires extensive customization and workarounds, which can be time-consuming and costly. Companies may need to invest in middleware solutions, API development, and data mapping to enable smooth data exchange and process coordination. These technical challenges can delay implementation timelines and limit the realized benefits of integration.
Resistance to Change
Implementing supply chain integration is not just a technical challenge; it also requires a significant shift in mindset and behavior. Internal stakeholders may be skeptical of the benefits or resistant to changing their established ways of working. Overcoming this inertia requires strong leadership, clear communication, and effective change management strategies.
Similarly, partners may be reluctant to fully embrace integration, particularly if it involves sharing proprietary information or adapting their own business processes elsewhere. Building trust, aligning incentives, and demonstrating the mutual benefits of collaboration are key to securing partner buy-in and commitment.
Cybersecurity and Data Privacy Risks
As supply chains become more digitally interconnected, they also become more vulnerable to cyber threats. Integrating systems and sharing data across partners increases the potential attack surface for malicious actors. A breach at any point in the network can compromise sensitive information, disrupt operations, and damage reputations.
Moreover, the handling of personal data in the supply chain context raises important privacy concerns. That’s why it’s crucial to invest in employee training and support their pursuit of cybersecurity certifications. Using resources like the Security+ Practice Test and Dumps can equip professionals with a solid understanding of protecting sensitive data and securing interconnected systems effectively. Companies must ensure compliance with evolving data protection regulations, such as GDPR and CCPA, when exchanging customer or employee information with partners. Failure to implement proper safeguards and governance can result in legal liabilities and loss of customer trust.
Compliance and Regulatory Hurdles
Supply chain integration often spans multiple regions and industries, each with its own specific compliance and regulatory requirements. Navigating this complex landscape can be a significant challenge, particularly for companies operating in highly regulated sectors such as healthcare, food and beverage, or aerospace.
Ensuring that all partners adhere to the necessary standards and certifications can be a time-consuming and resource-intensive process. Companies may need to conduct extensive audits, implement strict quality control measures, and maintain detailed documentation to demonstrate compliance. Failure to meet these requirements can result in penalties, reputational damage, and supply chain disruptions.
Scalability and Adaptability Issues
While supply chain integration can enhance efficiency and agility, it can also create challenges in terms of scalability and adaptability. As the network grows and becomes more complex, it may become increasingly difficult to onboard new partners or expand into new markets. The need for extensive integration and customization can slow down the production process, and limit flexibility.
Executives Prioritize Supply Chain Agility:
According to a survey conducted by McKinsey, 93% of senior supply-chain executives intend to make their supply chains far more flexible, agile, and resilient.
Moreover, deeply integrated supply chains may struggle to quickly adapt to changing market conditions or strategic priorities. The rigidity of established processes and dependencies can hinder the ability to pivot or innovate in response to new opportunities or disruptions. Companies must strike a balance between the benefits of integration and the need for agility in an ever-evolving business landscape.
Resilience Lags:
According to PwC’s 2023 Digital Trends in Supply Chain Survey, only 30% of executives prioritize enhancing resilience as a critical goal when making investments in supply chain technology.
How Supply Chain Integration Works: Key Processes and Technologies
Tech Drives Supply Chain Efficiency:
63% of organizations have implemented technological solutions to monitor and assess the efficiency of their supply chains.
Integration of Planning Processes
Effective supply chain integration starts with aligning planning processes across the supply chain refers all partners. Two key frameworks for integrated planning are Sales and Operations Planning (S&OP) and Collaborative Planning, Forecasting, and Replenishment (CPFR).
S&OP is a monthly or quarterly process that aligns demand, supply chain process, and financial plans. It brings together stakeholders from sales, marketing, operations, finance, and the supply chain to create a single, unified plan. By collaboratively reviewing forecasts, capacity, inventory, and financial targets, S&OP helps balance supply and demand while optimizing resources and profitability.
CPFR takes S&OP a step further by involving external partners like suppliers and customers. It’s a shared process where all parties agree on joint business plans, synchronize forecasts, and coordinate replenishment. CPFR improves visibility, reduces forecast error and inventory, and enhances responsiveness to demand changes. Walmart’s collaboration with P&G is a classic CPFR success story.
RPA is Expected to Transform Supply Chains:
In a 2022 survey, 60 percent of organizations from different industries worldwide revealed that they expect robotic process automation to have a major or moderate impact on supply chains by 2025.
Case Study: Procter & Gamble and Walmart
Procter & Gamble and Walmart’s CPFR partnership led to a 10% reduction in forecast error and a 15% reduction in inventory levels. This collaboration demonstrates the benefits of integrating planning processes across partners.
Integration of Execution Processes
Integrating execution processes is critical for turning plans into reality. Order management, fulfillment, logistics, and transportation must be tightly coordinated across the supply chain.
Order Management and Fulfillment
With integrated order management, all partners have real-time visibility into orders, inventory, and shipments. This enables them to quickly process orders, allocate inventory, and track fulfillment status. Advanced ship notices (ASNs) and electronic proof of delivery (ePOD) further streamline receiving and reconciliation.
Efficient fulfillment relies on optimizing inventory placement, pick/pack processes, and delivery options. Leading companies use network modeling, multi-echelon inventory optimization, and dynamic safety stocks to position the right products in the right places. Distributed order management intelligently sources orders based on inventory availability, shipping costs, and delivery times.
AI and Analytics Investment:
According to KPMG, through 2024, 50% of supply chain organizations will invest in applications that support artificial intelligence and advanced analytics capabilities.
Logistics and Transportation Management
Integrating logistics and transportation across the supply chain network is key for reliable, cost-effective product flows. This involves holistic planning of inbound, outbound, and reverse logistics, considering constraints like capacity, costs, lead times, and service levels.
Transportation management systems (TMS) are the backbone for optimizing modes, carriers, and routes. By aggregating demand and sharing loads, companies can improve utilization and secure better rates. Real-time visibility solutions track in-transit shipments, predict ETAs, and proactively mitigate disruptions.
Innovative fulfillment models like cross-docking, merge-in-transit, and postponement help cut costs and compress cycle times. Sharing logistics assets and collaborating on last-mile delivery further elevate performance.
Example: DHL’s Integrated Logistics
DHL’s integrated logistics solutions have helped companies like IKEA achieve a 25% reduction in transportation costs and a 10% increase in on-time delivery rates.
Enabling Technologies for Integration
Underpinning supply chain integration is a range of enabling technologies:
Electronic Data Interchange (EDI)
EDI has long been the standard for exchanging business documents like purchase orders, invoices, and shipping notices. By replacing paper-based transactions with standardized electronic formats, EDI automates processes, reduces errors, and speeds up communication. Despite the rise of newer technologies, EDI remains entrenched, especially among larger companies.
API-based Connectivity and Web Portals
APIs (application programming interfaces) allow different systems to talk to each other and share data in real time. They enable more flexible, granular integration compared to batch-oriented EDI. Many supply chain software vendors now offer API libraries for connecting with partners’ systems.
Web portals, also known as partner portals, provide a user-friendly interface for partners to view data, place orders, and collaborate on processes. They can be quickly set up without deep integration. However, portals often require manual effort and lack advanced functionality.
Blockchain for Secure Multi-Party Collaboration
Blockchain is an emerging technology that enables secure, transparent, and tamper-proof record-keeping across multiple parties. It can track the provenance and movement of products, verify certifications, and execute smart contracts. By creating a single source of truth, blockchain enhances trust, accountability, and automation among supply chain partners.
Prominent blockchain consortia in the supply chain space include TradeLens (shipping), IBM Food Trust (food safety), and MediLedger (pharmaceuticals). While adoption is still nascent, blockchain holds immense potential to transform supply chain collaboration. According to a study, the global blockchain market in supply chain management is projected to grow from $145 million in 2020 to $3.5 billion by 2026, at a compound annual growth rate (CAGR) of 53.1%.
By integrating processes and leveraging these technologies, companies can achieve true end-to-end supply chain visibility, agility, and optimization. However, the integration process is a complex, iterative journey that requires aligning people, processes, and systems across the ecosystem.
5 Steps to Implement Supply Chain Integration
Step 1: Assess current state and define vision
Before embarking on supply chain integration, it’s crucial to understand your current supply chain landscape. This involves mapping out existing processes, systems, and relationships across the entire supply chain network. By creating a comprehensive picture of the as-is state, you can identify pain points, bottlenecks, and opportunities for improvement.
Next, define a clear vision and set integration goals and objectives that align with your overall business strategy. Consider questions such as: What are the desired outcomes of integration? How will it enhance customer value, operational efficiency, and competitive advantage? Engaging key stakeholders in this visioning process helps build consensus and commitment.
Step 2: Identify integration partners and scope
With a vision in place, identify and prioritize integration partners based on their potential impact and readiness. Focus on partners that have the greatest influence on your supply chain performance and customer experience. Assess their technological capabilities, process maturity, and willingness to collaborate.
Define the depth and breadth of integration for each priority partner. Depth refers to the level of information sharing, process coordination, and decision synchronization. Breadth involves the range of functions and activities to be integrated, such as demand planning, inventory management, and logistics. Strike a balance between integration benefits and implementation complexity.
Prioritization factors for integration partners
-
Strategic importance and long-term value
-
Impact on key performance metrics
-
Technological compatibility and maturity
-
Relationship strength and trust level
-
Resource availability and change readiness
Step 3: Establish governance and performance metrics
Effective supply chain integration requires robust governance structures and aligned performance metrics. Institute cross-functional and cross-company teams to oversee integration efforts. Assign clear roles, responsibilities, and decision rights. Establish communication protocols and conflict resolution mechanisms to foster collaboration and trust.
Develop a balanced scorecard of shared key performance indicators (KPIs) that reflect integration objectives. These may include metrics related to on-time delivery, inventory turns, cash-to-cash cycle time, and perfect order fulfillment. Align incentives and rewards with these KPIs to drive accountability and continuous improvement across the integrated supply chain.
Step 4: Design and deploy integrated solutions
With partners, scope, and governance in place, it’s time to design and deploy integrated supply chain solutions. Start with pilot projects to test and refine integration approaches before large-scale rollout. This allows for learning and adaptation in a controlled environment.
Implement solutions in a phased manner, focusing on highest-impact areas first. Ensure adequate resources, training, and support are in place to drive adoption and mitigate risks. Leverage technology enablers such as cloud platforms, APIs, and blockchain to facilitate seamless data exchange and process coordination.
Key considerations for integration solution design
-
Interoperability external integration and scalability of technology architecture
-
Data quality, security, and governance standards
-
Process standardization and exception handling
-
Change management and user experience design
-
Rollout strategy and hyper-care support model
Step 5: Monitor and continuously improve
Supply chain integration is an ongoing journey, not a one-time event. Continuously monitor integration performance using established KPIs and identify improvement opportunities. Conduct regular business reviews with your supply chain managers and integration partners to discuss progress, challenges, and best practices.
Assess supply chain integration maturity periodically and benchmark against industry peers. Use frameworks such as the Supply Chain Operations Reference (SCOR) model to guide capability development. Invest in talent, technology, and processes to drive integration excellence and agility in the face of changing business conditions.
Is Supply Chain Integration Right for Your Business?
Aligning Supply Chain Integration with Strategic Objectives
Before embarking on supply chain integration, it’s crucial to evaluate if it aligns with your company’s strategic objectives. As Michael Porter, a leading authority on competitive strategy, states, “The essence of strategy is choosing what not to do”.
Integrating your supply chain can yield significant cost savings and benefits, but it also requires substantial investment and organizational change. Ensure that pursuing integration supports your long-term goals and aligns with your core competencies.
Assessing Industry Dynamics and Competitive Position
Your industry’s characteristics and your company’s competitive position should inform your decision to integrate. In stable, predictable industries, tight integration can lead to efficiency gains. However, in rapidly evolving sectors, flexibility may be more valuable than integration.
As Sunil Chopra and Peter Meindl explain in their book “Supply Chain Management: Strategy, Planning, and Operation,” “The responsiveness required for each company’s supply chain depends on the supply and demand uncertainties the company faces”.
Analyze your industry’s supply and demand uncertainties to determine the appropriate level of integration for your business.
Evaluating Resource Constraints and Capabilities
Supply chain integration demands significant resources, including technology investments, process redesign, and talent development. Honestly assess your company’s capabilities and constraints before committing to integration.
As noted in a Deloitte report on supply chain integration, “Companies often underestimate the complexity and cost of integration, leading to delays, cost overruns, and suboptimal results”.
Carefully evaluate your company’s readiness to undertake the challenges of integration. Consider starting with smaller pilot projects to build capabilities and demonstrate value to other stakeholders before scaling up.
Engaging Trusted Advisors and Building a Business Case
Given the complexity and potential risks of supply chain integration, engaging trusted advisors can provide valuable guidance. Supply chain consultants, industry peers, and academic experts can offer insights and best practices to inform your decision-making.
As Tom Linton, Chief Procurement and Supply Chain Officer at Flex, advises, “Collaborate with partners who have deep expertise in supply chain integration. Their experience can help you navigate the challenges and unlock the full potential of integration”.
Ultimately, the decision to pursue supply chain integration should be based on a solid business case that quantifies the expected benefits, costs, and risks. Work with your finance and operations teams to develop a comprehensive analysis that supports informed decision-making.
By carefully evaluating strategic alignment, industry dynamics, resource constraints, and engaging trusted advisors, you can determine if supply chain integration is the right path for your business. A thoughtful, data-driven approach will position you for success in your integration journey.
Making Supply Chain Integration Work for Your Business
Supply chain integration offers significant benefits like improved visibility, efficiency, and customer service. But it also comes with risks like high costs, dependency on partners, and change management challenges.
To determine if supply chain integration is right for your business, carefully evaluate your strategic objectives, industry dynamics, and resource constraints.
Key considerations include:
-
Identifying high-impact integration opportunities with key partners
-
Establishing clear governance structures and performance metrics
-
Designing phased implementation plans with adequate support
-
Monitoring performance and driving continuous improvement
If supply chain integration aligns with your goals and capabilities, it can be a powerful tool for staying competitive in today’s fast-paced, global business environment.
What’s one step you can take this week to explore supply chain integration opportunities for your organization? Perhaps scheduling a brainstorming session with your team or reaching out to a trusted advisor for an initial assessment.